This Gates-backed startup makes chemicals from carbon emissions
Hundreds of millions of tons of plastic and polyester are made each year from hundreds of millions of tons of ethylene—a chemical currently produced from fossil fuels that has a massive carbon footprint. But a startup called Dioxycle is making ethylene from recycled carbon emissions and renewable electricity instead.
“Chemicals have this incredible decarbonization potential, in terms of the impact, and right now they’re overlooked,” says Dioxycle cofounder and CEO Sarah Lamaison. The startup says its technology can make chemicals that compete on cost with the fossil-based versions. It just raised $17 million in a Series A funding round co-led by Lowercarbon Capital and Breakthrough Energy Ventures Europe (the latter of which was founded by Bill Gates).
The team designed a custom electrolyzer, with modules that stack together and use electricity to split CO2 and produce carbon-based chemicals, beginning with ethylene. The details of the process are proprietary, but the company says that it uses little energy, and it believes it’s the lowest-cost approach that exists to make ethylene sustainably.
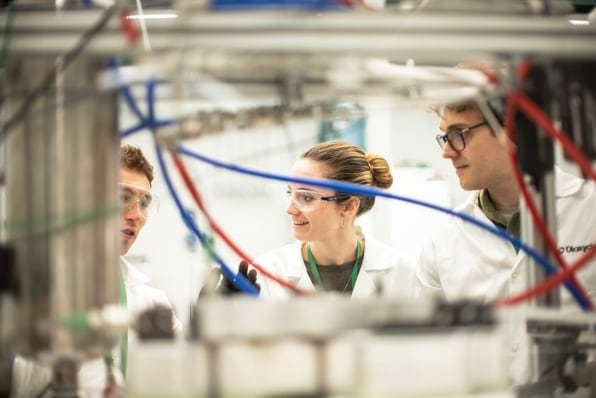
After scaling up from lab trials to its first prototypes last year, Dioxycle will use the new funding to build industrial-scale equipment. (One electrolyzer will have the same ability to convert carbon as 20,000 trees.) The plan is to work with partners in the chemical industry to place the equipment in existing factories, where companies can use their own emissions as inputs; other sources of captured CO2 can come later, including CO2 captured directly from the air.
“We see ourselves as a technology provider to existing chemical manufacturers,” Lamaison says. “Our goal is really not only to innovate on the electrolyzer itself but also on the way we integrate our system within existing industries.” It’s not possible to scale up as quickly as needed, she says, without making as much use as possible of the infrastructure that already exists.
Helping the industry make the switch could eliminate hundreds of millions of tons of CO2 emissions a year. The key to making that possible, Lamaison says, is how quickly the cost of renewable electricity can continue to fall.
Of course, reducing the emissions from products like plastic, polyester, and PVC doesn’t eliminate another challenge: what happens to those products when they’re eventually thrown away.
“Any plastic product is going to be creating microplastic pollution indefinitely, for as long as it exists on the planet,” says Jennifer Congdon, deputy director of Beyond Plastics, a nonprofit that advocates for eliminating plastics. “I think that projects like this draw the attention away from the need to reduce our use of plastic in every possible way.” We need to do much more to question our dependency on plastic in the first place, she says.
Lamaison agrees that the world needs to move away from disposable plastic packaging. But for other uses, like lightweight car parts, plastic is the best available option. From a practical standpoint, the $180 billion ethylene market isn’t likely to disappear immediately—and with a very limited window of time to tackle climate change, the new tech could help reduce emissions nearly the size of those from the airline industry.
Arguably, there’s room for both approaches: moving away from plastic and other ethylene-based products as quickly as possible while also developing tools to help the industry change.
(28)